TABLE OF CONTENTS
WHAT IS A STERN TUBE BEARING?
A stern tube bearing is a precision-made component that is used to support the propeller shaft and transfers the radial forces acting on the propeller to the ship’s structure. The bearing allows the propeller shaft to rotate with as less friction as possible.
Stern tube bearings are of the slide bearing type (also referred to as journal bearings or plain bearings). The bearings are located inside the stern tube of the vessel, therefore the name stern tube bearings. The amount of bearings used in a stern tube varies, but a set-up of one aft bearing and a forward bearing is a common solution.
A stern tube is a precisely machined weldment consisting of several tubes, the bearings are press-fitted into the stern tube. To be able to transfer the bearing forces to the vessel, stern tubes are installed in the ship’s structure. This can be done by a combination of resin casting and a bolted connection, or by welding.
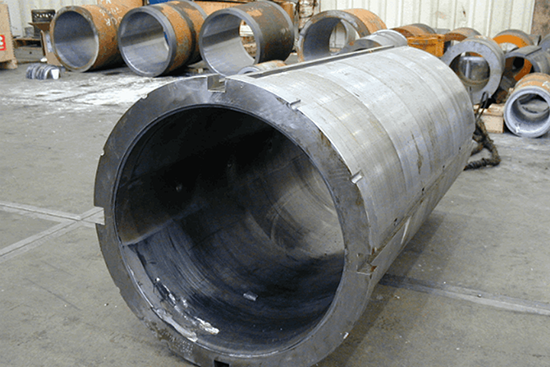
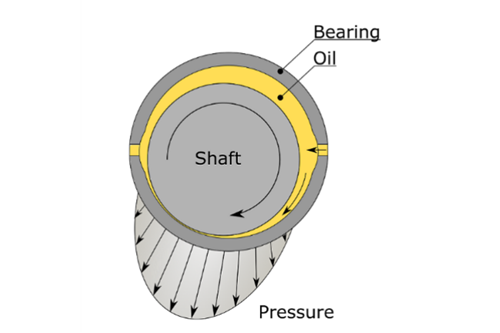
HOW IT WORKS
The function of the stern tube bearings is to carry the radial loads of the propeller shaft and to protect the shaft against wear. In case of an oil-lubricated bearing, this is achieved by creating an oil film between the bearing and the propeller shaft. When the propeller shaft is rotating, nearby oil will follow the circumferential movement of the propeller shaft. At sufficient shaft speed, the oil will flow from the supply holes in the bearing along with the shaft towards the bottom of the bearing. Here it is forced between the narrowing space between bearing and shaft, which creates lift. When the shaft speed is high enough, there will be no metallic contact between the shaft and bearing. This principle is called hydrodynamic lubrication LAGERSMIT STERN TUBE BEARINGS MATERIALS AND OPTIONS:
Lagersmit delivers stern tube bearings suitable for oil-lubricated systems.
Shaft diameters can vary from 70mm till approx. 900mm.
The bearings are made out of a cast iron bush with a white metal lining on the inside.
There are two types of white metal; lead based and tin based. In most cases lead based white metal will be sufficient for stern tube bearing applications and will also be the most economic option. For ice-class, navy vessels or environmental regulations we recommend tin-based white metal lining. Tin based white metal is more suitable when dynamic loads can occur.
WEAR DOWN
Bearing wear of an oil lubricated stern tube bearing is generally small. However, it is required to monitor bearing wear to ensure safety and satisfactory operation in the future. Bearing wear down measurements can be done by measuring the distance from the aft seal housing parts to the shaft by means of a Vernier caliper. When the initial value during seal installation is known, the deviation of the following measurement can be translated to bearing wear. Bearing wear down measurements can be performed with Lagersmit type of seals.
Note that water lubricated bearings are different, wear rates of these bearings are much higher.
HOW TO REDUCE FRICTION / WEAR?
It’s very important to choose the correct configuration of the bearing, key parameters are:
Viscosity of the lubricantShaft speed
Bearing load
Bearing dimensions
Note that most of the bearing wear will occur at lower shaft speeds or when the bearing is under high loads, e.g. start-up, extreme manoeuvres, mooring. During sailing there should by hydrodynamic lift in the bearing and therefore no metallic contact and low friction.
CLASSIFICATION
Lagersmit bearings can be delivered with a class certificate upon request.
LAGERSMIT
Did you know our company name is derived from the Dutch word ‘lager’, which means bearing? It’s time to highlight were it all started: the bearings. Since 1856 we have been delivering high quality castings and from the 1960s we expanded our product range with sealing solutions. This blog focuses on the bearings and gives you more information about the working principles, how our bearings deliver you Peace of Mind and what the advantages of using white metal lining are.
OPTIONS:
Aft, an intermediate of forward stern tube bearings.Temperature sensor for measuring bearing metal temp;
Different grades of cast iron
Different types of white metal, including lead- and tin-based white metal.
Delivery in pre-machined condition, with or without oil supply holes and longitudinal grooves.
Bearings can be delivered with class approval upon request.